Continuing with the blacksmithing theme, I made a hot cutter for my hardy hole.
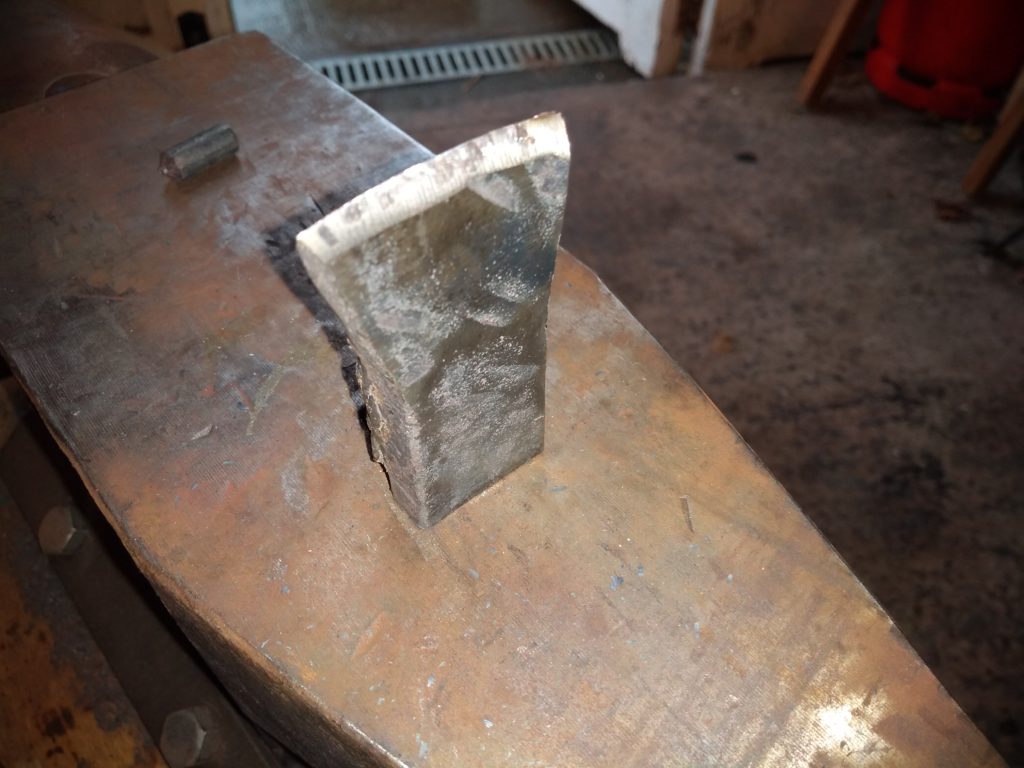
This was quite an easy thing to make.
Firstly, I got a bit of tough steel – in this case it was a piece cut off some heavy duty Ford Transit leaf springs. I really don’t know what steel they are made from. It should be heat treatable – it is after all spring steel, but as I’m using it for hot working the heat treatment doesn’t matter so much (i.e. it won’t stay heat treated for long…). It is, however, quite tough stuff.
I started out with a piece which had been cut from the thinnest portion of the spring and it was rounded on one side. So the first couple of heats were taken up with scraping the road grime from the surface and squaring up the rounded portion while keeping the steel flat overall.
Once I’d got it to an approximate shape, I held the steel in tongs at the edge of the anvil and hammered half on, half off. This gave the taper and also the fan effect. I’m not trying to forge a perfect flat, square edged chisel, the fan and the curve at the top all help when using it. The curve means you can drop it into a groove and angle the work to extend the groove.
Anyway, once I’d got a bevel approximately hammered in – incidentally with some awful fishlips – I allowed it to cool while using the bandsaw to cut a piece of 20mm box section to approximate length and cutting a triangle out of the end to allow it to taper out of the hardy hole.
I then welded the whole mess together. My welding is really rough, but I think it is improving a little – at least I’m quite confident it won’t fall apart.
Then it was just a few heats while I hammered the box into the hardy hole in all the different orientations until it dropped in nicely and could be removed easily. It is interesting the way that the tight hot fit becomes a usable fit when cold.
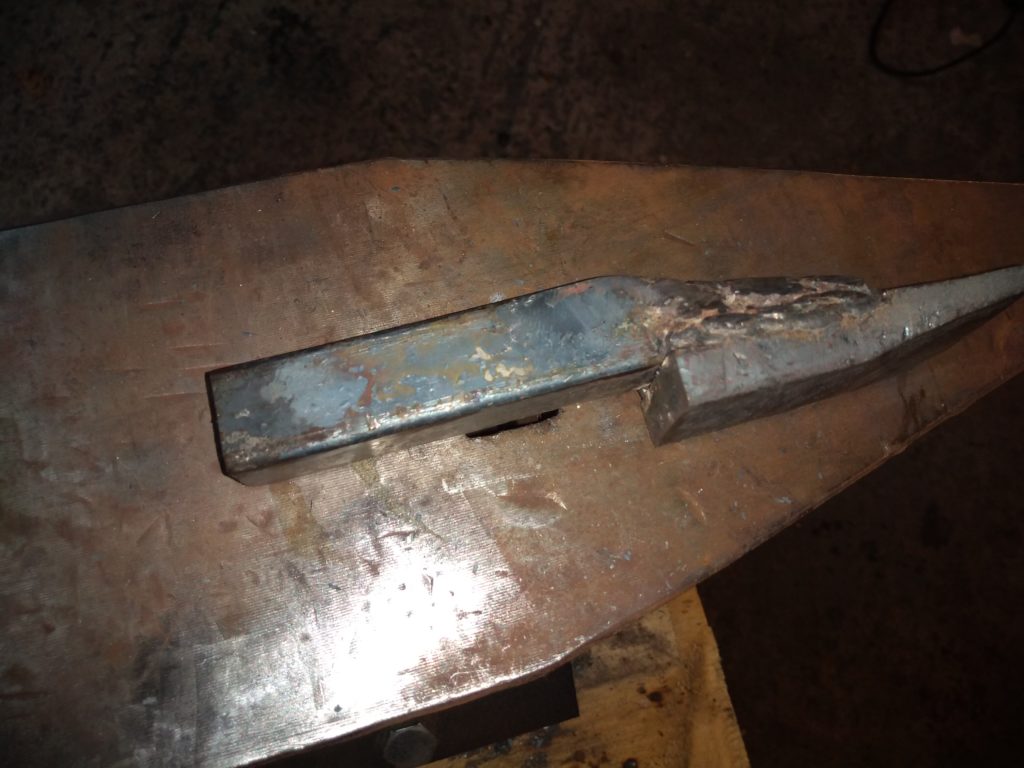
Then I ground in some bevels aiming for about 30 degrees. I’ve not measured it, but it seems about that.
Using a hot cut hardy is interesting. It is, after all, just a chisel which is held by your anvil. So far I’ve been cutting over the side of the anvil, but that ends up squishing the work where it is cut, kinda like those straws full of sherbert. You can’t easily recover the end to a nice shape.
When using the hot cut, you use a lot less force. It is a series of little taps rotating the work each time. The chisel creates a wedge shaped cut by moving the material. Eventually when it is cut off you end up with a conical end.
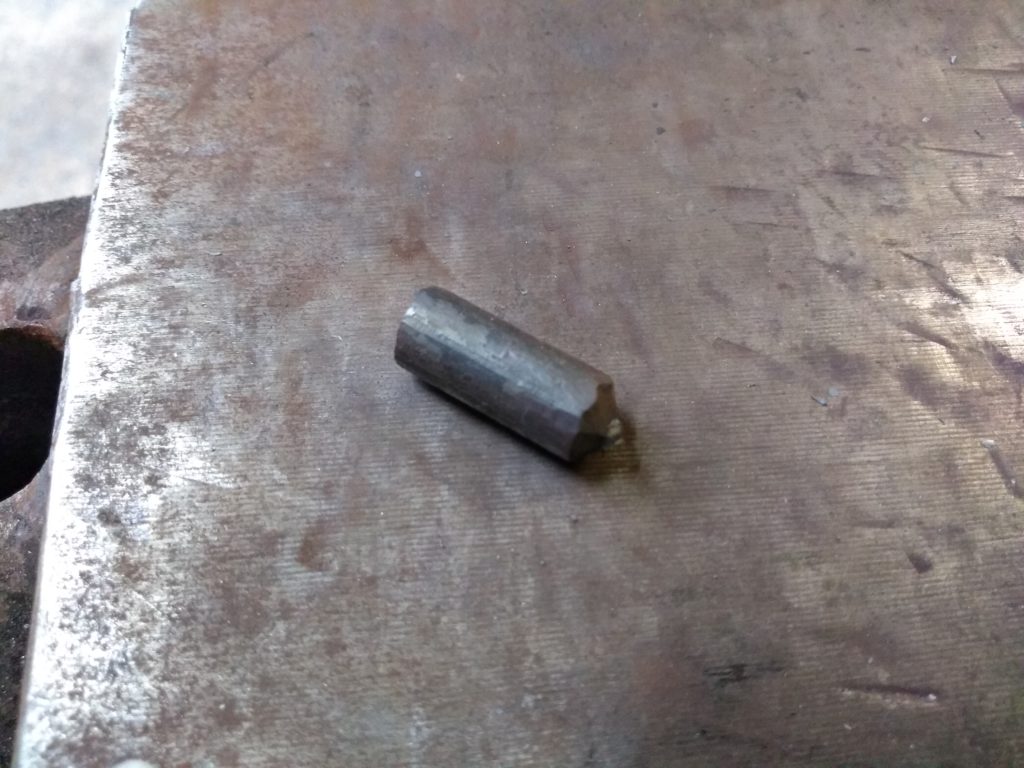
This is lovely to work with. It forms a really good start for hammering in a taper. If you start a taper on a square saw cut then the edges stretch out before the middle does and it is really easy to get fish lips which might need filing out or cutting off later.
With the tapered hot cut end you can start forging down on the shoulder of the conical part and it will stay conical. It would be hard to get the shape badly wrong.
I’m enjoying making hardy hole tooling. It is very satisfying when you drop the tool freely into the hole and it feels solid and reliable yet comes out easily.